─AD─
COVID-19パンデミックを経て見えた
近未来のワクチン製造施設のあるべき姿
ザルトリウス・ステディム・ジャパン
ワクチン製造施設は大きな変革が求められている。COVID-19のパンデミックによって、従来の製造設備が抱えていた課題が浮き彫りとなったためだ。次のパンデミックが発生しても、しっかりと対応できるようにするためには何が必要なのか。
150年以上にわたり、ライフサイエンス分野を支え続けるリーディングカンパニーであるザルトリウス・ステディム社のFluid Management Technologyアプリケーションサービス アジアマネージャーのJulius Ang氏とアプリケーションスペシャリストの千手昌平氏に話を聞いた。
■パンデミック下では製造施設の柔軟性が特に重要
従来、ワクチン製造施設では、インフルエンザワクチンや定期接種ワクチンの製造に特化した設備で、安定的な生産が行われていた。しかし、予期せぬ感染症が蔓延した際には、複数のワクチン開発が同時に進められるため、どのワクチンを製造することになるか不明なケースもあり、従来型の製造施設では対応が難しいということが、今回のパンデミックを通じて確認できたという。つまり、異なる種類のワクチンを迅速に大量生産できる柔軟な生産体制が求められるようになったわけである。
千手氏は、従来のワクチン製造施設と今後求められるワクチン製造施設との違いについて、図1を示しながら説明した。従来のワクチン製造施設はDesign 1、プラント1ではワクチンA、プラント2ではワクチンBというように、各プラントで製造するワクチンが決まっている最も柔軟性の低い形であるとした。この形では、状況に応じて生産ラインを追加して生産能力を拡大するといったことは難しい。
それに対し、Design 2では1つのプラントで異なる種類のワクチンが製造できるように設計され、柔軟性が高くなっている。これを実現するための重要なキーの1つが、ボールルームコンセプトである。固定された装置のない広大なスペースに、目的のワクチンを製造するシングルユース機器を、必要な分だけ配備するという考え方だ。
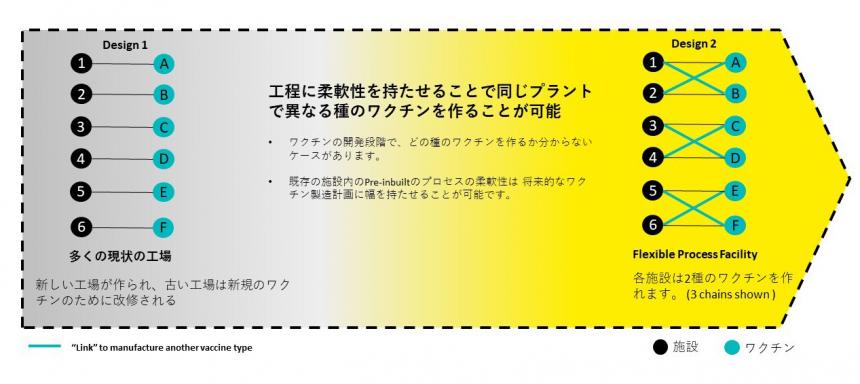
「従来のワクチン製造施設では、製造ラインごとに共通のミキサーやタンクなどの固定設備がある培地調製室、培養室、精製室、さらに充填室といった部屋を備え、それぞれの部屋を行き来する際に更衣が必要となるため、手間も時間もかかっていました。ボールルームコンセプトを採用すれば、類似したプロセス・ステップで共通の機器を利用し、共有することで、より多くの機器が適合し、より少ないスペースでスケールアップすることが容易になります。もちろん、更衣室やエアーロックを削減できるので、省スペース化にもつながります」(千手氏)。
「特定のワクチン製造工程内での柔軟性は、異なるワクチン製造工程間でも同様の柔軟性を拡張して提供できます。図1の『Design 2』の性質上、さまざまなワクチン製造計画の "ボールルーム"の共通性からそれらを応用することが可能です。そこで、さらに選択したワクチン候補の製造で、スケールアップとスケールアウトに焦点を絞ります」(Julius氏)。
同社は、ボールルームコンセプトの具現化に必要なシングルユース製品や、プロセス解析を容易にする各種システムを提供しており、ワクチン開発から生産まですべてのプロセスをカバーすることができる(図2)。
「ボールルームコンセプトを採用するにあたっては、装置選定も重要なポイントです。多品種のワクチンの迅速な生産を可能にするためには、シングルユース装置や関連する消耗品にも柔軟性が求められるからです。例えば、当社の製品『Flexsafe® Pro Mixer』は、1つのドライブユニットで50Lから3,000Lまでのタンクに対応できるようになっています。また、消耗品については、お客様のプロセスごとに必要な部材を組み合わせキットとして提供することも可能です。各部材は、組み合わせを変えれば他のプロセスでも使用することができるようになっています」とJulius氏は話し、幅広いラインナップと、同社製品の柔軟性、ワンストップ管理ソリューションをアピールした。
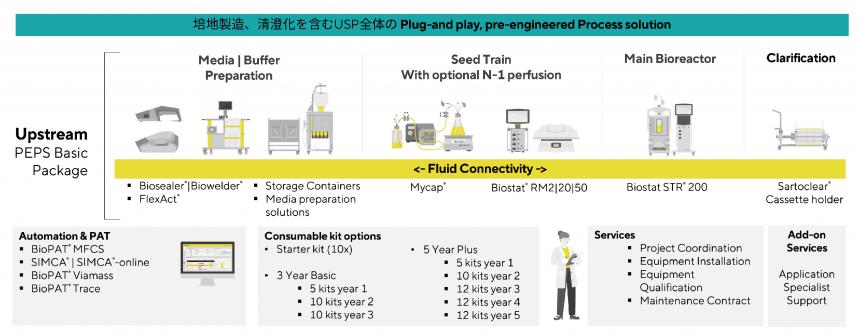
■シングルユース製品を安定的に供給できる生産体制を構築
コロナ禍において、シングルユース製品の長納期化が問題となった。同社では、その原因を分析し、2つの方向から問題の解決を図っている。1つはすべての製品群で生産能力を強化することである。将来の需要拡大を見越して、同社はすでに生産拡大に着手しており、2026年にはシングルユース製品が4倍の生産量になる見込みだという。
もう1つは、カスタマー・サプライ・プログラム(CSP)という取り組みである。顧客との連携により、顧客の見通しを継続的に分析し、それに応じて同社の生産計画を調整し、需給比率を安定させる自動化プログラムである。顧客は、注文した製品の生産状況をオンラインで確認できるようになっており、納期の透明性も確保されているという。
■サステナビリティへの取り組みも必要
ワクチン製造施設の将来像を考えるうえでは、環境負荷低減を図るなどのサステナビリティを考慮することも必要である。ザルトリウスグループとしては、CO2排出量を削減しつつ成長を続けていくことを目指していることから、利益当たりのCO2排出量を重視し、年間10%ずつ削減させ、30年までに70%削減(19年比)することを見込んでいる。
「ヘルスケア分野のCO2排出量は、地球全体の排出量の約4~5%を占め、そのうちの約0.025%がザルトリウスグループからの排出量と算出されています。当社の活動が及ぼす影響は比較的小さいですが、環境負荷を低減することは、顧客の環境問題対策をサポートし、医薬品製造をこれまで以上に環境に配慮したものにするという点で、重要なステップであると考えています」(Julius氏)。
「生物学的製剤の製造では、大量の水を消費します。ステンレス製設備ではCIP/SIPが必須ですが、その工程で使用する水の量は、製造プロセスにおける使用量の80%を占めています。シングルユース製品はCIP/SIPが不要なので、水の使用量の大幅な削減が可能となり、サステナビリティにつながるというわけです(図3)」と、千手氏はシングルユース設備を使用することがサステナビリティに寄与することになると強調する。
サステナビリティ関連の取り組みとして、同社では使用済みのシングルユース製品を回収し、リサイクルするという試みも行っている。回収したシングルユース製品をフィルムやチューブ、コネクタといったパーツごとに分けて粉砕し、その粉を原料として再利用というもの。現在は、実用化に向けてさまざまなデータを取得しながら、リサイクル素材を使用した製品を開発するための準備を進めているという。バイオ医薬品業界で環境の持続可能性を推進する同社の取り組みについてはこちらでも詳細している。
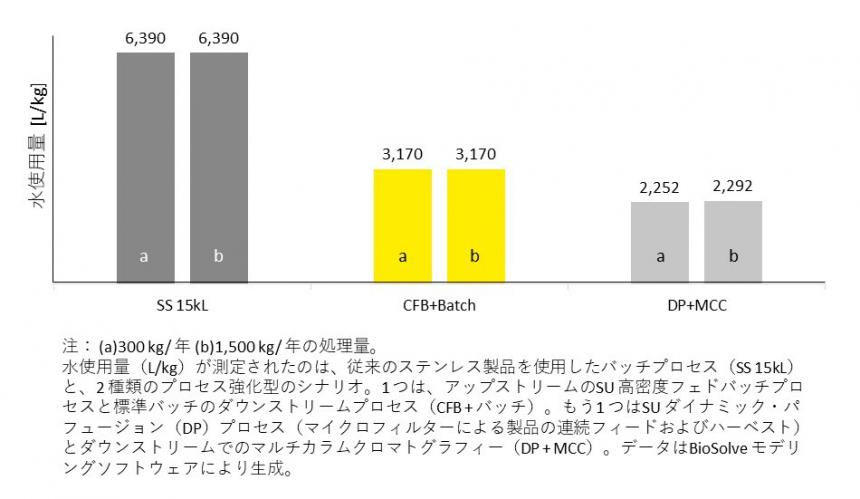
このように同社は、COVID-19パンデミックでの学びも生かしながら、将来のワクチン製造施設のあるべき姿を提案。これからも顧客から望まれるパートナーとなるために目指すべきゴールを共有し、そのゴールに向かって顧客とともに歩み続けたいとしている。
■この記事関連のWEBセミナーを2023年11月16日(木)に開催します。
「A Future-Ready Vaccine Facility『近未来のワクチン施設:次のパンデミックに向けた考察とギャップ』」
※インターフェックスWeek東京2023「技術セミナー」の拡大版
ウェビナー詳細・お申込みはこちら
■お問い合わせ
ザルトリウス・ステディム・ジャパン株式会社
〒140-0001 東京都品川区北品川1-8-11 Daiwa品川Northビル4F
E-mail:hp.info@sartorius.com
URL:https://www.sartorius-labsolutions.jp/