━AD━
製剤工程でのシングルユース活用
メリットを最大限に享受するためのキーポイントとは
メルク
2018 年11 月に行われた日本PDA 製薬学会第25 回年会のセミナーで、メルク株式会社プロセスソリューションズ事業本部の井出直人氏、矢吹知佳子氏が「製剤工程へのシングルユース充填アッセンブリの活用」について発表した。シングルユース(SU)導入にあたっては、設備と製品の相互作用評価や導入後を見据えた使用性の考慮など、幅広い視点での検討が必要になる。本セミナーでは、SU 導入を円滑に進めるためのポイントが整理された。
■時代ニーズに合致するシングルユースの特性
近年、SU 技術が急速に普及し、液剤の最終充填での活用(写真)も進んでいる。その理由には、製品開発期間短縮や生産工程の合理化、コスト低減といった業界ニーズに、SU 独自の利点が合致していることが挙げられる。最初に講演した井出氏は、「SU 化による大きな効果に残液の削減がある。バイオ医薬などの高価な製品が増加する中、これまで避けられなかったリットル単位での残液削減は、SU の導入/運用費を勘案してもコストメリットがある。また、ステンレスで必須となる洗浄・滅菌時間の省略やバリデーションの削減、コンタミリスクの排除、さらに可変性による工程のフレキシビリティもSU の利点」と総括した。
一方、これらメリットを享受するために検討すべき事項もある。「耐薬品性や溶出物/浸出物の評価が求められるほか、手作業による作業員の負担増もあるため、SOP での規定など、運用面も見据えることが重要。最終的には、考慮事項とメリットとのバランスを俯瞰して、導入を検討する必要がある」(井出氏)とした。
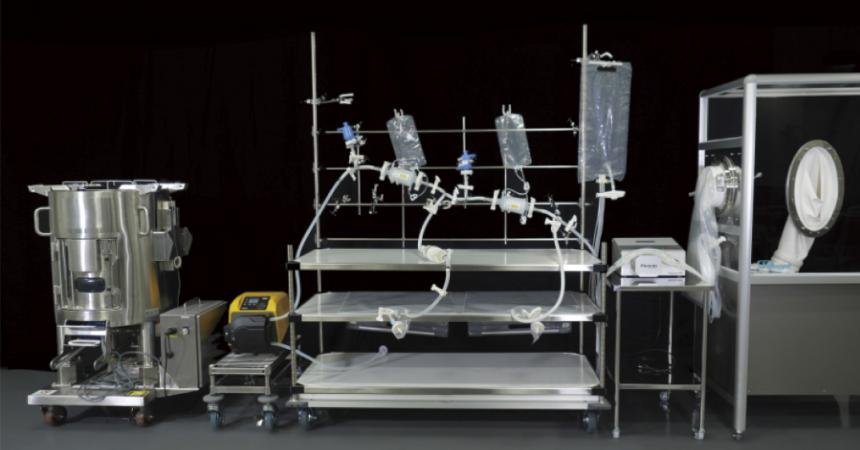
■実運用も見据えた具体的な導入フロー
続いて、導入フローの具体的な説明が行われた。「まず、剤形選択や充填機との兼ね合いの考慮、フィルターや充填ポンプ、チューブなど各パーツの選択を行い、アッセンブリをデザインする。その後、初期図面を作成し、試作でのテストを経て正式図面を完成させて納品に至る。多くの検討事項があるため、タイムラインが重要」と井出氏は指摘する。
講演ではこのフローに沿って、充填チューブの調整や撹拌条件検証、フィルター完全性試験の実施タイミングなど、“現場での実運用”を想定した検討について、事例を交えて解説された。
なお同社では、こうした検討を経た納品後も、設備装着から破棄までを適切に実施できるよう、作業員のトレーニングも行っているという。「実際に現場で“使える”ものを提供することを重視している」という言葉からは、“現場での実運用”を考慮して、トータルなサポートを行う同社の姿勢が垣間見えた。
■ バリデーション実施にはサプライヤーとの連携が必須
続いて、デザインや図面作成と併行して行うバリデーションについて講演した矢吹氏は、「図面が確定してからスタートすることが望ましいが、データ取得に時間がかかる項目もあるため、事前・追加評価の可能性も含めた全体的なタイムラインが重要」と強調し、実施の留意点を解説した。
EU-GMP ガイドラインや国内の製剤GMP などでは、製造設備が製品に影響を与えないことが要件とされており、現在改定中のEU およびPIC/S GMP Annex1ドラフト版でも「製品接触面に使用される材料と製品との適合性は、工程条件下で吸着や製品に対する反応性などを評価すること」との記載がされるなど、SU設備と製品の相互作用評価が重要視されている。
さらにユーザーには、化学的適合性や溶出物の評価に加えて、サプライヤーのクオリフィケーションも求められる。これは「工程自体をサプライヤーとともにつくる」というSU の特性によるもので、必要に応じてサプライヤーから品質証明書、完全性証明書などを入手し、変更管理の連絡も受けることが求められる。
このように、ユーザーとサプライヤーとの連携もバリデーション実施のポイントとなる。
■評価項目決定と各評価ステップ
矢吹氏は、代表的なアッセンブリ(撹拌、ろ過、充填)を例に、評価項目決定から実際の評価までの要点を示した。項目決定では、最終的な患者への影響を考慮することが必要なため、「接液するか否かや患者への影響の可能性などで部材を分類し、リスクに応じて必要な評価項目を決定する」という。
化学的適合性の評価においては、図面上で対象部材を確認、グループ化し、耐薬品性リストなどからすでに適合性のデータが存在するかを調査する。そして、データがない場合に新たに適合性試験を行う。なお、ユーザーは既存データの利用や試験実施をサプライヤーに依頼して、適合性証明書を取得することもできる。
溶出物/浸出物評価においては、リスクベースによる5 ステップのアプローチが推奨されている(図)。
「まずはプロセスを明確化してリスク評価の対象パーツを選ぶ。この際、接液面積が最大の部分をワーストケースとして対象をグループ化する。続いて溶出物の同定、定量化を行うが、詳細情報が得られれば、サプライヤー保有の一般データも使用可能である。3 つ目のステップとして、摂取量と許容曝露量との比較などから、溶出物についての安全性を確認する」(矢吹氏)。
ここまでで安全性が確保できれば不要だが、申請先国の求めや、その他のリスクアセスメント結果に応じ、ステップ4・5 として浸出物の評価と安全性再評価を行うこともある。
矢吹氏は、「ステップ3 または5 で安全性が担保できない場合は、運用方法を工夫しながら患者摂取量を減らし、最終的に安全性を確保できるようにする」と、運用方法も検討材料にしながら評価することが重要とした。
このようにSU 導入においては、さまざまな要素を検討する必要があるが、各要素の検討においては運用面を見据え、ユーザーとサプライヤーが手を携えることが重要になると言えよう。

【お問い合わせ】
メルク株式会社
〒153-8927 東京都目黒区下目黒1-8-1 アルコタワー5F
TEL:03-4531-1143
URL:www.merckmillipore.jp